Boosting Uptime for Compressor OEMCompressor Monitoring Solution
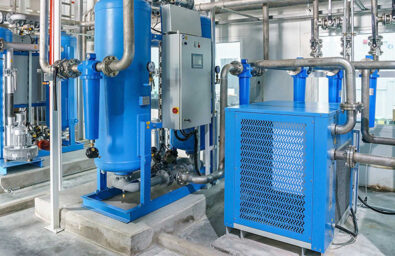
We are delighted to help our client, one of the top OEM of Hydraulic Boosters Compressor for Compressed Natural Gas (CNG) applications, having installed base of more than 500 compressors across locations.
The project was aimed at boosting uptime of compressors targeting lower operational expenses and spares consumption. The major pain point was system failure causing a direct impact on the revenue generation of the end client and the OEM.
Use Cases
- Maximize uptime
- Proactive maintenance
- Lower spare parts consumption
Challenge
OEM had a compression asset failure that interrupted service and had the potential to compensate customer in the form of penalty and thus loss of revenue for OEM.
Customer
The customer is an OEM of Hydraulic Boosters Compressor for Compressed Natural Gas (CNG) applications. They have an installed base of more than 500 compressors stations in India helping India’s energy transition roadmap for a cleaner, greener India.
Solution
Kemsys delivered an end-to-end real-time compressor monitoring system i.e data acquisition from PLC to disseminating analytics and key business KPI’s to various stakeholders.
Local PLC to connect to a Modbus TCP Ethernet or RTU RS485 gateway to ingest data over 4G/3G/2G modem to transfer data to a remote monitoring system.
The compressor monitoring solution uses Microsoft Azure IoT Hub-based solution to acquire data, analyze data and drive proactive and corrective actions. Its objectives are to avoid compressor shutdown and to minimize failures.
Data Collected
- Downtime
- Fault Detection
- Specific Power Consumption
- Gas Meters
- Maintenance Requirements – MTBF & MTTR
Solution Maturity
Mature – the technology has been on the market for > 5 years
Operational Impact
- Ensured maximum uptime with proactive condition-based maintenance
- Lowered operational expenditure via improvements in reliability and lowered spares consumption