Hardware Devices Compliance, Standards, and Regulatory Requirements for the USA
- February 4, 2025
- Posted by: Anand Borad
- Category: Device Engineering
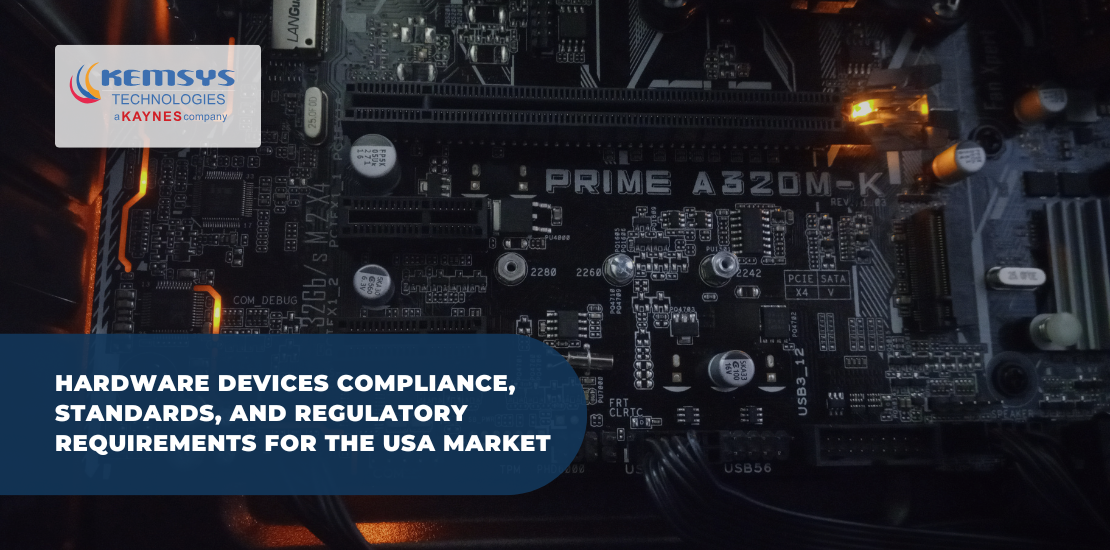
Bringing a hardware device to market is an exciting journey, but it comes with challenges that can be overwhelming for organizations.
Compliance plays a critical role in the process, from ensuring product safety to meeting the necessary regulatory requirements.
It’s not just about meeting legal requirements — it’s about protecting users, building trust, and ensuring your product’s success in the market.
However, many hardware compnies struggle to navigate the complexities around legal, safety, and regulatory requirements. Questions like “Do I need FCC certification for my device?” or “What safety standards must my product meet?” often arise, leading to long hours of research, discussions, costly mistakes, and delays.
The consequences of non-compliance can be severe—ranging from fines and product recalls to being banned from the market altogether.
This guide is written to make the compliance process simpler and more manageable for you. By following this guide, you’ll be able to make informed decisions and move forward confidently in your hardware product development journey.
Whether you’re working on a smart device, a medical gadget, or an industrial tool, we will help you understand key regulatory requirements such as
- FCC
- UL
- FDA
- Cybersecurity
- Environmental standards
- Labeling laws and more
Non-compliance isn’t just a risk; it’s a lost opportunity to build credibility and trust with your customers, retailers, and partners. By planning ahead and addressing compliance at the start, including design for manufacturing, you’ll avoid common mistakes, save time, and ensure your hardware device reaches the market smoothly.
This is your complete guide to understanding and navigating compliance, saving you time and effort while helping your product succeed. Let’s get started.
Understanding the Basics of Hardware Compliance
When designing and manufacturing a hardware device, compliance refers to meeting a set of standards and regulations established by federal, state, and industry bodies.
These standards ensure that your product is safe for use, operates as intended, and doesn’t harm the environment.
Compliance isn’t just a legal requirement—it’s a critical part of product development that can make or break your device’s success in the market. Implementing hardware design best practices can further enhance your product’s reliability and compliance readiness.
At its core, compliance addresses three key areas:
- Safety: Ensuring your device doesn’t pose a risk of harm to users. This includes electrical safety, fire hazards, and protection from physical injury.
- Environmental: Meeting standards that limit the use of hazardous substances, promote recycling, and reduce environmental impact.
- Operational functionality: Ensuring your device performs as expected without malfunctions or safety issues.
So why does compliance matter so much?
First things first, user safety is most important aspect.
A failure to comply with safety standards may lead to serious injuries or even fatalities in some cases, which jeopardizes your users as well as your company’s reputation.
Second, the non-compliance can lead to consequences such as fines, recalls, and potential lawsuits.
These can quickly wipe out your profits and damage your credibility.
While, a product that meets the necessary standards is viewed as trustworthy and reliable by consumers, retailers, and regulatory bodies.
It signals that you take quality and safety seriously – which helps to increase your product’s marketability.The
Cherry on the cake, compliance can open doors to important sales channels, such as large retailers or international markets, which may require proof of certification before they agree to sell your product.
Several key institutions ensure hardware compliance in the US, each with their own focus area:
- Federal agencies like the FCC (Federal Communications Commission) oversee communication standards
- FDA (Food and Drug Administration) handles medical device approvals
- The CPSC (Consumer Product Safety Commission) ensures product safety.
- Industry organizations such as UL (Underwriters Laboratories) and NIST (National Institute of Standards and Technology) set specific safety and performance standards that companies must follow.
- State regulators like the California Energy Commission set local standards – around energy efficiency and environmental impact.
Proactively understanding the basics of these requirements can save you time, money, and effort as you move forward in your product’s development.
Let’s dive into most important one by one, shall we?
1. Federal Communications Commission (FCC) Compliance
If you’re designing hardware devices that involve any wireless communication, it’s crucial to ensure FCC compliance.
FCC is a US government agency that regulates communication technologies, including radiofrequency (RF) devices. They ensure that devices don’t cause harmful interference to other communication equipment or public safety systems.
Simply put, if your device emits radiofrequency energy—either intentionally (like Wi-Fi and Bluetooth) or unintentionally (like many electronics) — it needs to comply with FCC regulations.
Who Needs FCC Compliance?
Any hardware device that transmits or receives signals using Wi-Fi, Bluetooth, NFC, cellular, or similar wireless technologies must meet FCC requirements.
But it’s not just high-tech gadgets like smartphones and wearables that fall under these rules.
Everyday products such as televisions, computers, and even microwave ovens (which emit low levels of RF energy) are also subject to FCC regulations.
That means, if your device operates using or interacts with wireless signals, it needs to comply with FCC guidelines.
Standards to Meet within FCC
To ensure compliance, devices must meet the specific standards set out in the FCC’s Code of Federal Regulations:
- Part 15: This section applies to most consumer electronics and specifies limits on the amount of RF energy a device can emit without interfering with other devices. If your product is a common consumer device—like a smartphone, tablet, or laptop—this is likely the section you’ll need to follow.
- Part 18: This applies to industrial, scientific, and medical devices that generate RF energy but are not primarily intended for communication purposes. For example, certain medical equipment or industrial machines that use RF to power a specific function will need to meet these standards.
How to Achieve FCC Compliance
Achieving FCC compliance involves several steps to ensure that your device doesn’t exceed the permissible levels of RF emissions. Here’s how you can get there:
- Testing at an Accredited Lab: Conduct testing at an FCC-accredited lab to ensure your device meets the required standards. These labs perform the necessary tests to measure RF emissions and ensure your product doesn’t cause interference.
- Obtain an FCC ID: Once your device passes the necessary tests, you must apply for an FCC ID. This unique identifier allows the FCC to track compliance for each specific device model.
- Label the Product: You must label your product with the FCC ID and other required information, such as the compliance statement (e.g., “This device complies with Part 15 of the FCC Rules”). This lets consumers and regulatory bodies know that the device has been tested and approved.
- Provide Documentation: Along with the product, you will need to provide detailed documentation, including test reports, schematics, and the device’s technical specifications, to demonstrate compliance.
How to Simplifying the Process
- Work with a Compliance Consultant Early: Compliance consultants have the expertise to guide you through the process and help identify potential roadblocks before they become costly problems. Their advice can save time and ensure you don’t miss any important steps.
- Use Pre-Certified Modules: If possible, use pre-certified modules for wireless communication. These modules are already tested for FCC compliance, which can significantly reduce the time and cost of certification.
By ensuring your device meets FCC standards, you protect your brand, avoid penalties, and make your product more attractive to retailers and consumers.
FCC Compliance may seem like a complicated process, but with careful planning and the right guidance, you can navigate it successfully and bring your device to market with confidence.
2. Electrical Safety with UL Certification
When designing hardware devices, ensuring electrical safety is an equal priority. This is where UL certification comes into play.
UL (Underwriters Laboratories) is a globally recognized independent safety certification organization that tests products to meet strict safety standards, particularly concerning electrical hazards, fire prevention, and overall safety.
UL certification confirms that your product is safe for consumers and free from electrical and fire risks, making it a critical step in the compliance process for many hardware devices.
What is UL Certification?
UL certification involves thorough testing to ensure your product meets a range of safety standards.
This can include evaluating the device for electrical safety, fire resistance, safe operation, and the ability to handle potential environmental stresses like overheating or short circuits.
For hardware devices, particularly those involving electricity or battery power, UL testing ensures that your product poses no risk to users and performs safely over time.
While UL certification is not always legally required, it’s highly valued in the industry and often necessary for getting your product on the shelves.
Retailers, distributors, and even insurance companies typically require UL certification before they stock or sell your device.
It assures them that your product has been tested for safety and meets established safety standards, which ultimately boosts consumer trust in your product.
Why UL Certification is Important
UL certification is considered a best practice for safety. Here’s why it’s so important:
- Retailer Requirements: Many retailers won’t stock a product unless it has UL certification. They need the assurance that it’s safe and won’t cause harm to their customers.
- Consumer Trust: A product bearing the UL mark is recognized as safe by consumers, helping to build credibility and trust in your brand.
- Liability Protection: By meeting UL standards, you reduce the risk of accidents and product recalls, which could have serious financial and reputational consequences.
How to Get UL Certified
Getting your product UL-certified involves several steps, typically managed through a Nationally Recognized Testing Laboratory (NRTL).
These labs are authorized by OSHA (Occupational Safety and Health Administration) to carry out safety testing and certifications. Here’s how the process works:
- Submit Your Product: Submit your hardware device to an NRTL for evaluation. The lab will test your product against the relevant UL safety standards for its category (e.g., electrical safety, fire prevention).
- Address Feedback: The lab will provide feedback on any issues found during testing. If the product doesn’t meet the standards, you’ll need to make adjustments and resubmit it for further testing.
- Get Certification: Once your product meets the required safety standards, you’ll receive the UL certification. Your device can then carry the UL mark, signifying it’s been tested and approved for safety.
Common Mistakes to Avoid for UL Certification
While UL certification is a crucial part of product development, many hardware manufacturers make mistakes that delay or complicate the process. Here are some common pitfalls to avoid:
- Ignoring Safety in Early Designs: Incorporating safety considerations from the very beginning of your design process is essential. Failing to do so could lead to design changes and additional testing later on, adding time and cost to your certification process.
- Underestimating the Time and Cost: UL certification can take time—sometimes several months—and it can be expensive. Be sure to budget for these costs and plan the timeline accordingly to avoid delays in product launch.
Achieving UL certification not only helps your product meet safety standards but also plays a key role in establishing your brand as reliable and consumer-friendly.
By prioritizing safety early in the design process and working with an accredited lab, you can ensure your device is ready for the market and well-received by consumers.
3. Consumer Product Safety Commission (CPSC) Compliance
The Consumer Product Safety Commission (CPSC) is a US government agency responsible for ensuring that consumer products meet safety standards and do not pose a risk of injury.
While CPSC oversees a wide range of products, it plays a particularly significant role in regulating electronics and children’s products.
As an entrepreneur or manufacturer, understanding CPSC compliance is essential to ensuring your product meets safety requirements and avoids any legal or reputational issues.
CPSC Overview
The CPSC was established to protect consumers from products that could cause unreasonable risks of injury or death.
The agency enforces safety standards for many types of consumer goods, including household electronics, furniture, toys, and even clothing.
For electronics, which are increasingly involved in our daily lives, CPSC regulations ensure that devices are safe to use and don’t present electrical or fire hazards.
Similarly, for children’s products, the CPSC ensures they are safe from choking hazards, toxic materials, and other potential dangers.
Key Responsibilities of CPSC
CPSC’s primary responsibility is to enforce the Consumer Product Safety Act (CPSA), which requires manufacturers to meet specific safety standards for their products. The agency is also responsible for:
- Testing and Certification: The CPSC oversees the testing of products to ensure they meet safety standards. This includes issuing safety certifications to manufacturers after successful testing.
- Product Recalls: If a product is found to be hazardous, the CPSC can mandate a recall, requiring the manufacturer to remove the product from the market and offer refunds or replacements to consumers.
By complying with CPSC guidelines, you demonstrate that you take consumer safety seriously, which builds trust with both consumers and retailers.
Special Considerations for Children’s Products
For children’s products, such as toys, children’s electronics, and baby gear, the CPSC sets even stricter safety standards.
Children are more vulnerable to potential hazards due to their smaller size and developing bodies. Products designed for children must comply with additional regulations, including:
- Child-Resistant Packaging: Products like cleaning supplies or medicines must be packaged in ways that are difficult for children to open.
- Lead and Phthalates Limits: Products for children must adhere to strict limits on harmful substances like lead and phthalates, which can have long-term health consequences.
- Small Parts Regulations: Toys and other children’s products must be free of small parts that could be a choking hazard.
In addition to meeting general safety standards, products intended for children must also obtain a Children’s Product Certificate (CPC).
This certificate verifies that the product has been tested for safety and meets all required regulations before it can be sold.
Steps for CPSC Compliance
To ensure your product complies with CPSC standards, follow these steps:
- Understand Relevant Safety Standards: Familiarize yourself with the specific safety standards that apply to your product category. For example, toys have different safety standards than electronics or household appliances.
- Test Products with a CPSC-Accepted Lab: The CPSC requires that products be tested by a CPSC-accepted lab. These labs are certified to conduct the required safety testing to confirm that your product is safe for consumers.
- Obtain Certification: After your product passes testing, you can obtain the necessary certifications, such as the Children’s Product Certificate (CPC) for children’s products or general product safety certifications for others.
Compliance with CPSC regulations ensures that your product is safe, trustworthy, and legally compliant.
By prioritizing safety and working with accredited testing labs, you can avoid costly recalls, fines, and damage to your brand.
4. Environmental and Sustainability Standards
As consumers become more environmentally conscious, there’s growing demand for eco-friendly products.
From reducing carbon footprints to ensuring responsible disposal, manufacturers need to consider environmental impact at every stage of product development.
Complying with environmental and sustainability standards not only helps your product align with consumer preferences but also ensures compliance with regulatory requirements both in the US and globally.
Why Environmental Compliance Matters
Today’s consumers are not just looking for quality; they are also seeking products that align with their values, especially around sustainability.
Environmentally responsible products—whether through the materials used or their end-of-life disposal—have a significant market advantage.
Moreover, environmental compliance is increasingly being mandated by law. The US has several important regulations that impact hardware design and manufacturing, and many global markets have similar requirements.
Whether you’re designing an electronic gadget, home appliance, or industrial machinery, ensuring your product complies with environmental standards is no longer optional; it’s a necessity.
Key Environmental Compliances and Regulations
Several key regulations govern the environmental standards for hardware devices. Here’s an overview of the most significant ones:
↠ RoHS (Restriction of Hazardous Substances)
RoHS is a regulation that limits the use of certain hazardous substances in electronic and electrical equipment. These substances include lead, mercury, cadmium, and other materials known to be harmful to the environment and human health.
Compliance with RoHS is mandatory for any device that falls under its scope, which includes many types of consumer electronics. It ensures that these substances are eliminated or minimized, thus making products safer for both users and the planet.
↠ California Proposition 65
This law mandates that products sold in California carry a warning label if they contain chemicals that are known to cause cancer, birth defects, or other reproductive harm.
The list of chemicals covered by Proposition 65 is extensive and regularly updated.
While California-specific, it can impact any product sold in the state, and failure to comply could result in legal action and loss of market access.
↠ WEEE (Waste Electrical and Electronic Equipment)
WEEE aims to reduce the environmental impact of electronic waste by encouraging the recycling and safe disposal of electronic products.
It places responsibility on manufacturers for the collection, recycling, and proper disposal of their products when they reach the end of their life cycle. In many regions, including the EU, compliance with WEEE is mandatory.
↠ Energy Star Certification
Energy Star is a certification that identifies energy-efficient products, particularly appliances, electronics, and office equipment.
Products that earn this certification meet strict energy efficiency guidelines set by the Environmental Protection Agency (EPA) and the Department of Energy (DOE).
For devices that consume significant power, obtaining Energy Star certification can improve marketability and lower operational costs for consumers.
How to Meet Environmental Standards
To ensure your product meets environmental regulations and resonates with eco-conscious consumers, consider the following strategies:
- Use Eco-Friendly Materials: Opt for sustainable materials in your product design, such as recyclable plastics, biodegradable components, or materials that have a low environmental impact. Prioritize non-toxic materials, especially in products like electronics and toys.
- Test for Restricted Substances Early in the Design Phase: Testing your product for compliance with RoHS and other substance restrictions should be done early in the design process. This way, you can identify and remove any non-compliant materials before the production phase, saving time and cost.
- Include Proper Labeling and Recycling Instructions: Products should come with clear instructions on recycling and disposal. This includes adhering to WEEE standards by marking your product with appropriate disposal symbols and including information on how to safely recycle or dispose of the product.
- Seek Energy Star Certification for Applicable Devices: If your product uses energy, consider testing it for Energy Star certification. This not only helps with marketability but also ensures that your device adheres to important energy-saving guidelines, making it attractive to consumers who are looking to reduce their energy consumption.
By meeting these environmental and sustainability standards, you not only comply with laws and regulations but also position your brand as a leader in responsible manufacturing.
Adopting eco-friendly practices, from sourcing materials to designing for the environment, can differentiate your product in a competitive market, ensuring both legal compliance and long-term success.
5. Cybersecurity and IoT Compliance
As the Internet of Things (IoT) continues to revolutionize the way we live and work, the cybersecurity of connected devices has become a critical concern.
IoT devices, such as smart thermostats, security cameras, wearables, and healthcare devices, are increasingly interconnected and share sensitive personal data.
This growing web of connected devices raises significant concerns around privacy, data security, and vulnerability to cyber-attacks.
In this section, we’ll explore the essential regulations and strategies for ensuring cybersecurity compliance in your IoT devices.
Growing Importance of IoT Security
The rise of IoT has transformed everyday products into sophisticated, data-collecting devices that communicate with each other and the cloud.
While this innovation offers unprecedented convenience and efficiency, it also introduces potential risks, including data breaches, hacking, and unauthorized access to personal or financial information.
Cyber-attacks on IoT devices can result in serious consequences, ranging from identity theft to breaches of national security.
Given the proliferation of connected devices and the associated security risks, regulatory bodies are tightening their oversight.
IoT security is no longer just a good practice—it’s a legal requirement. Compliance with relevant regulations not only safeguards your users but also protects your brand from costly reputational damage and legal liability.
Key Cybersecurity Regulations
Several laws and frameworks are in place to help manufacturers navigate the complex landscape of IoT security. Here are some of the most relevant ones:
↠ California SB-327 and Oregon IoT Security Laws
In response to growing concerns over IoT security, California and Oregon have enacted laws that specifically address the need for stronger protection in IoT devices.
California’s SB-327 mandates that connected devices have reasonable security features that are appropriate to the device’s nature and purpose.
This includes setting default passwords, ensuring the device can securely store personal data, and providing an option for updates. Similarly, Oregon has passed its own version of IoT security laws that impose similar requirements.
↠ NIST Cybersecurity Guidelines for IoT Devices
The National Institute of Standards and Technology (NIST) provides comprehensive cybersecurity guidelines that help manufacturers build secure IoT devices.
These guidelines focus on ensuring that IoT devices have the right levels of protection against threats, such as unauthorized access and data breaches.
NIST’s recommendations include secure device authentication, data encryption, and the ability to patch vulnerabilities through software updates.
These guidelines serve as an essential reference for manufacturers aiming to meet security and privacy standards.
↠ GDPR (General Data Protection Regulation)
For devices sold globally, particularly in the European Union, the GDPR is an important regulation to consider.
While primarily focused on data protection and privacy, the GDPR sets strict standards for how personal data is collected, stored, and shared.
IoT devices that handle personal information must comply with GDPR by ensuring data encryption, obtaining explicit user consent for data collection, and providing users with control over their data.
Non-compliance with GDPR can result in significant fines and loss of consumer trust.
Key Strategies for IoT and Cybersecurity Compliance
While compliance with these regulations is essential, here are some actionable tips to ensure your IoT devices meet cybersecurity requirements:
- Implement Strong Password Policies: One of the most common security vulnerabilities in IoT devices is weak or default passwords. Ensure that your devices are shipped with unique passwords, and implement mechanisms that encourage users to create strong, secure passwords. Additionally, consider enabling multi-factor authentication (MFA) for added security.
- Include Mechanisms for Software Updates: Cyber threats evolve over time, and your IoT devices need to be able to adapt. Design your devices with the ability to receive software updates that can fix security vulnerabilities. Make sure these updates are easy for users to install and are rolled out promptly when necessary.
- Test Devices for Vulnerabilities Before Launch: Conduct rigorous security testing on your devices before they hit the market. This includes identifying potential vulnerabilities and patching them ahead of time. Penetration testing, vulnerability assessments, and third-party security audits can help ensure that your devices meet the highest security standards.
By proactively addressing IoT security, you not only comply with regulatory requirements but also position your products as trustworthy and reliable in the eyes of consumers.
In a market where cybersecurity is increasingly a dealbreaker, focusing on security early in your product development lifecycle can help you avoid costly legal issues, recalls, and loss of market confidence.
6. Labeling Requirements and Intellectual Property
When it comes to launching hardware devices in the market, two critical aspects—labeling requirements and intellectual property (IP) protection—often determine your product’s compliance, market access, and long-term success.
Clear and accurate labeling ensures transparency and adherence to regulatory standards, while safeguarding your intellectual property protects your innovation from unauthorized use and imitation.
Labeling Requirements
Labels do more than just display your brand—they communicate essential information about compliance, safety, and product origin to consumers and regulators.
Meeting the right labeling standards is crucial to avoid penalties and ensure smooth market entry. Here are some of the key labeling requirements:
- FCC Labeling and Identification: Devices that comply with Federal Communications Commission (FCC) requirements must display an FCC label, which typically includes the FCC ID and a declaration of compliance. This label assures users and regulators that the product meets radiofrequency emission standards.
- Energy Efficiency Labeling: For devices like appliances, Energy Star labels or other energy efficiency markers are essential. These labels highlight the product’s environmental performance and appeal to eco-conscious consumers while meeting regulatory requirements.
- Country of Origin: Products sold in the United States must often include a country of origin label, such as “Made in the USA” or “Assembled in China.” This requirement helps inform consumers and ensures compliance with trade regulations.
Proper labeling is not just about compliance; it also builds trust with consumers, distributors, and retailers by showing that your product meets all necessary standards.
Intellectual Property Protection
The innovative features of your hardware device—be it design, functionality, or branding—are valuable assets that need protection from competitors.
Safeguarding your intellectual property (IP) is vital for maintaining a competitive edge and avoiding legal disputes.
- Register Patents: If your product includes a novel invention or technology, consider filing for a utility patent (for functional aspects) or a design patent (for visual elements). This grants you exclusive rights to manufacture and sell the invention for a set period.
- Secure Trademarks: Protect your brand identity by registering trademarks for your product name, logo, or tagline. A strong trademark distinguishes your product in a crowded market and prevents others from misusing your branding.
- Copyright Software: For products that involve proprietary software, such as IoT devices or apps, register your software under copyright law. This ensures you retain ownership and control over how it is used or distributed.
Best Practices for IP Protection
To avoid pitfalls in IP protection, follow these best practices:
- Conduct an IP Audit Before Production: Before launching your product, perform a thorough audit to identify all elements requiring IP protection. This ensures no aspect of your innovation is left unprotected.
- Work with an IP Attorney: Navigating the legal intricacies of patents, trademarks, and copyrights can be complex. Collaborate with an experienced IP attorney to streamline the process and avoid potential infringement issues.
By adhering to labeling regulations and protecting your intellectual property, you not only meet legal requirements but also create a strong foundation for your product’s market success.
A properly labeled product that showcases compliance and innovation inspires confidence among stakeholders, while robust IP protection safeguards your ideas for the future.
7. FDA Compliance for Medical Devices
Medical devices are among the most highly regulated products in the United States.
The Food and Drug Administration (FDA) oversees their safety and efficacy to ensure that devices used in healthcare do not pose risks to patients or users.
If your hardware device falls into the category of medical devices—like health monitors, wearables, or diagnostic tools—meeting FDA compliance is essential before it can enter the market.
When is FDA Approval Needed?
The FDA regulates devices that are intended to diagnose, prevent, or treat medical conditions. Whether your device requires approval depends on its classification and intended use.
Products like wearables that monitor health metrics, diagnostic tools, or therapeutic devices will likely require some form of FDA oversight.
Key FDA Requirements
Medical devices are classified into three categories based on their risk level:
- Class I (Low Risk): Includes simple devices like tongue depressors and manual stethoscopes. These typically require general controls and may not need premarket submissions.
- Class II (Moderate Risk): Includes devices like blood pressure monitors and infusion pumps. These require a Premarket Notification (510(k)), demonstrating that the device is substantially equivalent to an already legally marketed device.
- Class III (High Risk): Includes critical devices like pacemakers and deep-brain stimulators. These require a Premarket Approval (PMA), a more rigorous process involving clinical trials to prove safety and effectiveness.
Steps in FDA Compliance
Here’s how you can navigate the FDA approval process:
- Determine Device Classification: Assess the risk level and intended use of your device to identify whether it is Class I, II, or III. Use the FDA’s product classification database for guidance.
- Conduct Clinical Testing if Required: For Class III devices, and sometimes Class II, clinical trials are necessary to validate safety and performance. Partner with certified testing organizations to ensure compliance.
- Submit Applications to the FDA: Depending on the classification, file the appropriate documentation—either a 510(k) or a PMA. This submission should include test results, device descriptions, and manufacturing details.
Meeting FDA compliance ensures your medical device is safe and effective for users, while also protecting your business from potential recalls or legal issues.
With proper planning and adherence to FDA guidelines, you can confidently bring your innovation to the healthcare market.
8. Import/Export and State-Specific Regulations
Expanding your hardware business often involves navigating the complexities of import/export regulations and varying state-specific rules.
These regulations ensure that products meet safety, environmental, and trade standards while preventing legal or financial setbacks.
Understanding and complying with these requirements is crucial for smooth operations, especially in the highly regulated US market.
Import/Export Compliance
When bringing hardware devices into or out of the United States, compliance with federal regulations is essential. Here’s what to consider:
- Work with US Customs and Border Protection (CBP): CBP oversees import and export activities, ensuring that goods comply with US laws. This includes correct tariff classifications, proper documentation, and adherence to applicable product standards. Engage with CBP early to avoid delays or penalties.
- Export Administration Regulations (EAR): Managed by the Bureau of Industry and Security (BIS), EAR governs the export of technology and devices. Depending on the nature of your product, you may need an export license, especially for items considered dual-use (civilian and military applications).
To streamline the process, consider hiring a customs broker or leveraging automated trade compliance software to manage documentation and track regulatory changes.
State-Specific Regulations
In addition to federal regulations, states often impose their own standards, particularly for energy efficiency, recycling, and safety. Keeping track of these can be a challenge:
- California Energy Commission (CEC) Standards: California requires hardware devices like appliances and electronic equipment to meet strict energy efficiency standards. Products failing to comply cannot be sold in the state.
- New York’s Electronics Recycling Mandates: New York mandates manufacturers to facilitate the recycling of electronic waste. This often involves participating in or funding take-back programs for used devices.
Challenges of State-by-State Variation
One of the most significant hurdles for manufacturers is the variation in state regulations. A standard compliant in one state may fall short in another, requiring adjustments to product design, labeling, or distribution strategies.
- Solution: Develop a centralized compliance strategy that considers the most stringent state regulations as a baseline. Engage with compliance consultants to monitor changes in state laws and adapt quickly.
Navigating the maze of import/export and state-level requirements demands careful planning but is key to ensuring your product’s marketability. By staying informed and proactive, you can avoid costly setbacks and ensure your devices meet all necessary standards.
9. Testing Best Practices and Common Pitfalls
Testing is the backbone of hardware compliance, ensuring that your product meets safety, environmental, and regulatory standards.
A robust testing strategy not only facilitates smoother approvals but also helps in identifying and addressing potential issues before they escalate.
However, navigating the testing phase requires careful planning and an understanding of common pitfalls.
Best Practices for Testing
- Choose Accredited Testing Labs:
Partner with Nationally Recognized Testing Laboratories (NRTLs) or other accredited labs. These labs are authorized to conduct compliance testing for standards like FCC, UL, or FDA, ensuring that your results are credible and accepted by regulatory bodies. - Budget for Multiple Rounds of Testing:
Testing is rarely a one-and-done process. Plan for iterative testing, especially for complex devices, to address feedback and implement required adjustments. This avoids delays during the final certification stage. - Start Testing Early:
Incorporate compliance testing during the prototype phase, not as an afterthought. Early testing identifies potential issues in the design stage, saving time and cost compared to resolving them after mass production begins. - Maintain Open Communication with Labs:
Share your product’s intended use, materials, and specifications with the lab upfront. Clear communication helps labs tailor their tests to your product’s specific requirements, reducing missteps and retesting needs.
Common Pitfalls to Avoid
- Insufficient Documentation:
Missing or incomplete documentation is one of the most common reasons for testing failures. Ensure that all technical files, user manuals, and compliance declarations are up-to-date and accessible during testing. - Rushed Compliance Testing:
Trying to squeeze compliance testing into tight timelines often leads to errors, increased costs, and project delays. Allocate sufficient time for testing and troubleshooting in your project plan. - Ignoring Updates to Regulations:
Regulatory standards evolve, and using outdated criteria can result in non-compliance. Regularly monitor changes in relevant standards and incorporate them into your testing protocols.
By adhering to these best practices and being mindful of common pitfalls, you can streamline the testing phase, reduce delays, and ensure your hardware device complies with all necessary standards.
Testing done right is an investment in your product’s success, safeguarding your business from costly recalls, fines, or market rejections.
↠ Simplifying Compliance for Your Hardware Device
Navigating the compliance landscape for hardware devices might seem like a daunting journey, but with the right approach, it becomes a manageable—and even strategic—process.
Early planning and consulting with industry experts can turn potential roadblocks into stepping stones for success.
As we’ve explored throughout this guide, understanding and meeting regulatory requirements such as FCC standards, UL certifications, FDA approvals, and state-specific rules is critical.
Whether you’re addressing environmental sustainability, cybersecurity, or labeling standards, each step adds value to your product, ensuring safety, reliability, and trust in the marketplace.
Take Proactive Steps Today
- Draft a Compliance Checklist: Break down all applicable standards and regulations into actionable items. A comprehensive checklist will serve as your roadmap, ensuring no requirements are overlooked.
- Start Testing and Certification Early: Incorporate compliance considerations during the design phase. Engage with accredited testing labs, and allocate time for potential iterations. Early testing minimizes costly last-minute changes and delays.
- Engage with Compliance Consultants: For complex or niche products, working with compliance experts can save time and prevent costly mistakes. Their guidance ensures that your device is aligned with the latest regulations.
Compliance is far more than a legal necessity; it is the foundation of trust and marketability. A well-compliant product reassures consumers, attracts distributors, and opens doors to global markets.
By adopting a proactive and systematic approach to compliance, you’re not only safeguarding your business but also building a reputation for quality and responsibility.
Your journey to bringing a hardware device to market starts here. Take the first step today by prioritizing compliance—it’s an investment in your product’s success and your company’s future.