- November 16, 2022
- Posted by: Anand Borad
- Category: Device Engineering
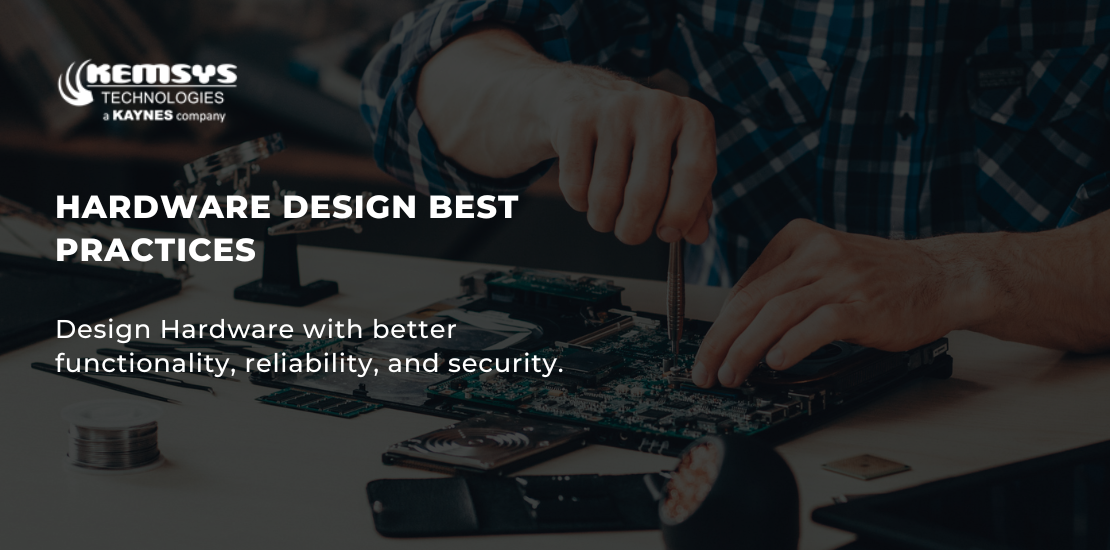
A successful hardware design meets the project requirements in terms of functionality, reliability, and security and is designed to work seamlessly within its environment.
Every design, – hardware or software – is subject to errors, insufficiencies, and mistakes. Yet, software design errors, however costly, can be managed with a software update without causing serious damage. But hardware errors are hard to fix, costly, and can have a long-term detrimental effect on the company.
In 2017, Spectre and Meltdown exploited inherent vulnerabilities in the core of modern processors such as Intel, AMD, and ARM. The discovery of a problem with Samsung Galaxy Note 7 batteries has the potential to dent a hole in the mobile giant’s brand. The mobile’s high combustion problems were zeroed down to the battery design and manufacturing process.
That’s the reason why a good hardware design is fundamental to the success of any product. Yet hardware design is complex, time-consuming, and resource-reliant. Moreover, the hardware design process should evolve, adapt, and adhere to standards from conception to deployment.
- Challenges of Hardware Design
- Industry-Led Best Hardware Design Practices
- The design review should be meticulous and cover all aspects of the design
- The component should be selected after evaluating its design, cost, availability, and lifecycle
- Consider the placement and compatibility of the components, technology, and systems
- Proper documentation is critical to any design project
- Sticking to the guidelines and standards eases the design process
- Making plans for contingencies is also important
- Build a feedback cycle within the system
- Conclusion
A hardware designer has to overcome a ton of challenges to execute a design properly. Let’s look at some of the design challenges before we explore the best design practices to adopt so that you don’t face a downside during the implementation stage.
Challenges of Hardware Design
One of the top challenges of developing a production-ready hardware design is providing the ability to support any future enhancements. The enhancements or changes could pertain to the design, functionality of the component, memory, power consumption, and more.
Some of the other challenges in hardware design include
There is no undo button
In hardware design, one of the biggest challenges is the lack of an option to undo the process.
Once the boards are soldered or the holes drilled, there is pretty much nothing you can do about it. This inability to rework makes the design that much more important.
A prototype could help in mitigating any rework, but there is no guarantee that a prototype will work exactly as anticipated during production.
Hardware design is a multi-layered process
Hardware design is a multi-layered process that has dependencies on several teams, such as engineers, technicians, designers, and more.
When compared with software design, hardware design has a significantly longer development cycle. A normal hardware design process could take months before it comes to fruition, and any changes or modifications are not likely to be solved overnight.
New technologies are always emerging
Keeping pace with the latest technological advancements in sensors, controls, motors, and processors is not an easy ask. There is always some new technology, better components, and new subdomains cropping up everywhere.
Design engineers need to have an understanding of these latest technologies to adapt and incorporate them into the design process.
Budgeting is a top priority
Another major challenge in hardware design is meeting the budget requirements. When focusing on designing the ‘perfect’ product, many times the budget takes a hit.
To counter these situations, designers would be forced to make changes to the design process, such as using a different type of material. While cost is a major business decision, it is incumbent on the designer to meet both the product and budget requirements seamlessly.
Large team size
It is not unusual for a hardware design team to have more than 30 designers with varying specializations. These interdependent teams branch out to work on several smaller elements in the design process and then flow back.
Managing large, diverse teams can be a logistical challenge. And, identifying the merging point can also play a critical role in the design process.
Industry-Led Best Hardware Design Practices
Due to the sheer complexity and challenges involved in the hardware design process, it is critically important to define a set of guidelines and follow the best practices for a better chance at success. Failing to follow the best practices could increase deployment time, development, and testing periods, which can escalate the cost manifold.
Some of the industry-tested and proven hardware design practices include,
The design review should be meticulous and cover all aspects of the design
The cost of errors is too high, and it warrants a thorough design review to make sure all the bases are covered properly.
If you don’t get a detailed design review, preferably by a third-party independent engineer, you are brewing a recipe for disaster.
No matter how great an engineer or designer you might be, every design should be scrutinized. Relying entirely on prototyping could increase the project cost, push deadlines, and take longer to get the product to market.
Getting a qualified second opinion is far cheaper and more beneficial than depending on prototyping.
The component should be selected after evaluating its design, cost, availability, and lifecycle
Before designing, consider component availability, design, cost, and lead times. When choosing critical components, thoroughly understand the datasheet and reference information to know the component limitations and capabilities.
If, for instance, you are working on PCB design, before designing the traces, you need to consider PCB production and PCB soldering. Understand the requirements such as minimum trace spacing, width, control capability, and more. You should also learn about the drill sizes, stencils, and soldering capacity. Selecting the components based on their capabilities might take some time, but it is worth the time and effort in the end.
Always keep a backup component that can provide similar functionality in case the one you’re using becomes obsolete or is no longer available.
Consider the placement and compatibility of the components, technology, and systems
A hardware design is never done in isolation. Hardware design and development is an iterative process that is dependent on several compatible components, systems, and technologies. Component placement is another critical element you should consider, as it impacts functionality, quality, and symmetry.
With new versions being rolled out now and then, it is important to design hardware that is compatible with the newer version of the firmware. It should also ideally work the other way around, where a newer version of the hardware should support the existing firmware version.
Proper documentation is critical to any design project
To make sure there is no ambiguity in understanding the requirements or developing the process flow, it is important to have detailed and meticulous documentation of the hardware design. The greatest upside of documentation is keeping an eye on the pain points, anticipating next-in-line processes, and adherence to guidelines.
The documentation also makes sure that both the hardware and firmware teams are on the same page. The document should ideally include high-level component details and design specifications, as well as low-level implementation information.
Sticking to the guidelines and standards eases the design process
Adherence to the standards ensures interoperability and functionality. The development standards you put in place should act as a guideline that has to be followed mandatorily. However, with time, standards evolve, and your hardware design solutions should also keep up.
Making plans for contingencies is also important
No matter how structured and streamlined your design planning is, you need a contingency plan in place.
What if the sensor doesn’t work?
What if the chips have failed?
It is not always possible to get a proper look at the chips or sensors since the hardware might pose visibility restrictions. The best workaround would be to design a debug hook into the device or build a logic analyzer into the chip.
Build a feedback cycle within the system
The hardware design should be evaluated internally and externally. It is also important to build a feedback cycle into the system as early as possible so that you can make the necessary engineering or component changes. Hardware design is an iterative process that thrives on feedback between engineers and the design team.
Conclusion
Keeping these proven best practices in mind during the hardware design services could help you mitigate some of the more critical challenges you might face. To help you stay away from design hiccups during your IoT hardware and smart product development projects, we at Kemsys, have put in place a streamlined and error-proof system that can get you the results you deserve.