Why Vibration Monitoring & Analysis Is So Important? How to do it?
- January 24, 2022
- Posted by: Manoj Pandey
- Category: Internet of Things

Here’s everything you need to know about monitoring machine vibrations in your plant
Has any doctor ever advised you to “listen to your body?” Do you know why they do that? Well, that’s because our body give some kinds of signals when something is not right with it. What if we told you that the same applies to machines as well.
Machines also provides many signs – omens, if you call it – before any big issue arises. One of those many omens are vibrations, also regarded as ‘machine vibrations.’ and’s appeal to your customers.
What are Machine Vibrations?
Let’s start with a simple definition of machine vibrations:
“Machine vibration can be described as the oscillation of a machine and its components relative to a reference plane of measurement.”
You can capture vibrations by depicting the machine’s amplitude on the y-axis and the x-axis representing the time. As vibration is a oscillatory motion, it forms a complex time waveform.
Here’s how it looks:
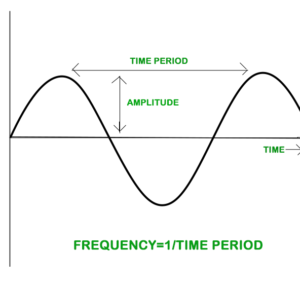
As you can derive from the graph, vibration isn’t just about the movement or displacement, but it’s also about its direction.
What Is Vibration Monitoring and Analysis?
Vibration monitoring and analysis is the process of capturing and analyzing the vibration levels and frequencies of a machine and then using that data to analyze the machine’s health and its components.
Why Monitor & Analyze Machine Vibrations?
As we saw previously, vibrations are symptoms that must be read by us so that we can make the machine work at its optimum. Here are four main reasons why we should monitor and analyze machine vibrations.
- They help identify the anomalies: As we discussed earlier, vibration monitoring is nothing but the diagnostic of a problem with the machine/ equipment. Thus, vibration monitoring can provide vital insights into component durability and changes to this pattern can indicate a failing component, often ahead of the time than when a human operator can begin to see a problem.
- Longer Machine Life: If you can solve the problems by analyzing the vibrations, you can fix them and help them run for a long duration. This means better Return on Investment (RoI) and lesser purchase expenses.
- Lowering Repair & Maintenance Costs: If there’s one thing that business owners absolutely hate, it’s maintenance costs. And they’re right as it’s frustrating to invest more and more money even though you’ve bought the best machinery. Machine Vibrations monitoring and analysis allows you identify the root cause of the machine operational issue before the need for a major overhaul, thus saving your money on repair and maintenance costs.
- Avoids Breakdown: Although vibrations are bound to occur in any machine, knowing the cause behind them is of paramount importance. You can ignore them at your own peril as it could be a symptom of a more significant issue that could cause a breakdown in the future. Monitoring and analyzing vibrations help prevent such serious consequences.
Where is Vibration Analysis Used?
Usually, Vibration analysis is carried out for condition monitoring on components of machinery and their critical rotating parts. These include:
- Bearings, gears, shafts, freewheels
- Gearboxes, motors, fans and drive-trains
- Piston engines, reciprocate compressors, pumps
Apart from machinery and rotating parts, it’s also used to monitor vibrations in bridges, pipes, turbine blades, etc.
How are Machine Vibrations Monitored?
Traditionally, an accelerometer has been Engineers’ go-to device to measure vibration data, but technological advancements have led to the inception of non-contact and high-performing sensors that go a step further. Examples include Piezoelectric (PZT) sensors, microelectromechanical sensors (MEMS), proximity probes, laser Doppler vibrometers, etc.
These sensors are quite easy to deploy and can be placed in the proximity of the bearing of the mechanical rotating equipment such as motor, pump, blower/fan, gearbox, spindle-bearing, etc. They produce an electrical signal proportional to the acceleration of the vibrating component to which the accelerometer or sensor is attached.
Next, the electrical signals are analyzed using various methodologies to study the vibrations and conclude.
Vibration Analysis Methodologies
As we saw previously, the electrical signals derived from accelerometers or sensors need to be processed to come to a conclusion. This is done using various methodologies, but mainly two approaches form the base of all:
Time-domain analysis: The time-domain analysis refers to the waveform when the amplitude is plotted against time. As it measures the amplitude, it can monitor vibration levels. So, when vibration levels go beyond the pre-defined limit, it means that the machine is not in good health, and there’s an underlying issue.
Frequency domain vibration analysis: Frequency domain analysis helps detect abnormal vibrating patterns. The waveform (amplitude vs. time) is subjected to spectrum analysis or FFT (Fast Fourier Transform)/ HFFT (Hexagonal Fast Fourier Transform) to do the frequency vibration analysis. This results in frequency vs. amplitude and can help discover the periodicity of the collisions.
Kemsys: Your Partner in Remote Vibration Monitoring & Analysis
We, at Kemsys Technologies, strive to provide one-stop-solution for your Vibration Monitoring and Analysis need – Sensors Engineering, Sensor Prototype,Testing/Certifications and Expert Data Analysis with advanced analysis technologies that include FFT, HFFT and Modal Analysis.
This helps you monitor, detect and identify anomalies in real-time so that you can prevent machine breakdown, and thus lower operation and maintenance costs, increased plant safety, productivity and higher ROI.